Curtain up on a special structure
With more than 70 teams and 1,400 players, the ZSC/GCK-Lions Organisation is one of the largest ice hockey organisations in Europe. They will soon have their own arena in Zurich-Altstetten. The arena has two rinks and a parking garage topped with a roof, which will also serve as a public terrace. The main arena is designed for about 12,000 fans. Making reference as much to the anticipated atmosphere as to the height of the building and its steep spectator seating, the site team have nick-named it the “Witches’ Cauldron”. Another rink, with room for 300 spectators, is used as a training hall and for matches involving juniors and lower-league teams. Outside the building, terraces and courtyards offer visitors additional space. Ice sports enthusiasts can gather there before and after a match – and particularly at breaks between playing periods – to discuss the action and sing celebratory songs. The ARGE ZSC Arena (Marti AG Zurich, Barizzi AG Bertschikon) consortium is contracted to construct the building ensemble.
Concrete curtain
One of the tasks is to construct the complex, fair-faced concrete facades. They are a particular feature of the building complex. While the longer sides are designed as concave waves, the shape of the north and south facades makes reference to a curtain. The facades incorporate glazed bull’s-eyes with a diameter of 2.00 m and lend the building a festive appearance. The arenas’ facades are constructed using in situ concrete and are not – as might be reasonably assumed for such a complex building – designed as prefabricated elements attached to the front of a load-bearing structure. The advantage here is that, if detailed and constructed perfectly, the walls will show no visible joints. However, this solution demands great skill and care from the site staff: there is no scope for a second chance. NOE is responsible for achieving the texture on the surface of the concrete facades.
On site
The requirements for the fair-faced concrete facades at the ice-sports arena are extremely high and everyone involved is committed to achieving a perfect result. The 200 or more concreting pours (horizontal and vertical construction stages) should be as uniform as possible, without visible joins where the formliners and stages butt up to one another. This was a good reason for the site team to concrete any large areas that are connected to one another all in one pour. The largest area poured was 21.70 m long and 11.59 m high. This required more than 50 formliners in different shapes and sizes up to 1.76 x 3.42 m and a weight of 590 kg. To avoid visible transitions between formliners as much as possible, all formliner butt joints were formed with formliners precut to the required sizes and the 5 mm and 7 mm wide joints filled and sealed with NOEplast filler.
Release agent is applied to the formwork or formliners before concreting to allow stripping. The consortium’s construction engineer tested release agents from different manufacturers in advance of the works. He decided to use NOE formwork wax, which produced the best results in the tests. “When stripping formwork, it is particularly important to choose the right time,” says Marcel Lappert, who manages the project for the ARGE ZSC Arena consortium. “At first we had some difficulties with this. If the concrete cures too quickly, a vacuum is created. We counteracted this by loosening the formwork after one day. To separate the concrete from the formliners, we used special cushions. These were put in place and slowly filled with air.” A great advantage of NOEplast textured formliners is that they can be reused up to 100 times. This advantage was exploited on the ZSC-Lions project. Because of the special facade geometry, some formliners will probably be used up to 30 times.
Unique project
Up to now, NOE has produced 45 models and transported more than 200 formliners to the Zurich site in 40-tonne trucks. This is the largest single contract for textured formliners that NOE has ever received and completed. It was also an entirely new experience for the consortium’s construction engineer. Marcel Lappert says: “To prepare us for this task, we searched for similar projects with a view to finding out what difficulties we might encounter and how we could overcome them. But we found no comparable project anywhere in the world. Therefore, I am extremely proud that we are making such good progress and that everyone on site is committed to achieving the required high quality.”
The Swiss Life Arena has now been opened. It is a powerful attraction for sports fans, event-goers and lovers of architecture.
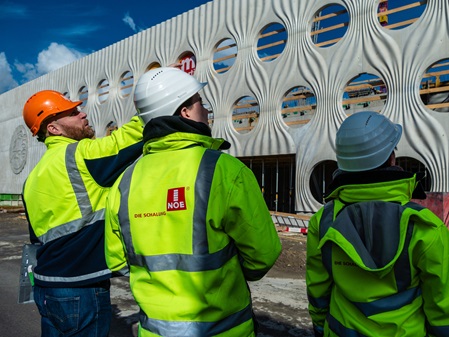
"To prepare for this task, we searched for similar projects. We wanted to gather information in advance about the challenges that may arise and how to solve them. However, we couldn't find a comparable project worldwide. Therefore, I am extremely proud that we are making such good progress with the work and that everyone on the construction site is so dedicated to achieving the required high quality."
Project Manager Marcel Lappert